impact testing composites|impact testing examples : importing This study presents types of damages in composite materials, impact damage and its classification in composite materials. Typical composite structures used in A380-800 commercial aircraft [19]
19 de out. de 2023 · If you want to use VR to practice for job interviews, there are some tips and steps to consider. First, choose a VR device that fits your budget and preferences, such as Google Cardboard, Samsung .
{plog:ftitle_list}
13 de jan. de 2023 · Pra mim esse é o vídeo mais pesado do portal do Zacarias, Pela brutalidade e violência dos bandidos, eles não tiveram misericórdia de ninguém, eu li sobre esse caso no TikTok, é pelo que li, os traficantes enganaram a loirinha falando que ela seria libertada se cooperasse, eles também prometeram não mexer com a família dela, pra .
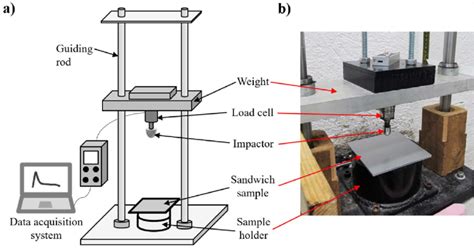
This review provides an overview of experimental impact testing and numerical impact simulations for composite materials in terms of a complementary combination of both techniques. It discusses the significance .
Impact testing of composite materials. Dr. Donald F. Adams (Wyoming Test Fixtures (Salt Lake City, Utah) discusses the methods for . Composites testing system configured for compression after impact (CAI) testing at temperature. Photo Credit: Instron Compared to traditional structural materials, polymer matrix composites (PMC) offer greatly .
Alignment is critical for composite testing applications because composites are anisotropic and generally brittle, as the anisotropy means that the properties and strength of the material differ depending on the direction of the applied force or load. . Impact test specimen types include notch configurations such as V-notch, U-notch, and .
The scientific community has taken a particular interest in the study of low-velocity impact (LVI) behavior of fiber-reinforced polymer (FRP) composites due to its application across various domains. This study presents types of damages in composite materials, impact damage and its classification in composite materials. Typical composite structures used in A380-800 commercial aircraft [19] The type of matrix and the impact test method used for each composite are also listed in . Table 2. DOI: 10.1051/, 01003 (2017) 71090100. 109. MA TEC of Conferences matec conf/201 3. Data for validating the model was obtained by conducting impact tests on flat composite panels according to the ASTM D8101 standard test method [5] titled “Standard Test Method for Measuring the Penetration Resistance of Composite Materials to Impact by a Blunt Projectile”. This test method is designed for measuring the response of .
In order to enhance the impact damage tolerance of the composite specimens within this study, 0.6 mm thick metallic panels were added as the lower protective layers of the specimens (test configurations tc-5 and tc-6). Additional positive effects are a stiffening of the composite structure and, due to the plastic deformation of the panels, the ."Instrumented Drop Weight Impact Testing of Composite Materials," Department Report UWME-DR-301-108-0 University of Wyoming (December 1983). Google Scholar Stellbrink, K.K. and R.M. Aoki. "Effect of Defect on the Behaviour of Composites," Progress in Science and Engineering of Composites, T. Hayashi, K. Kawata and S. Umekawa, eds. ICCM-IV .
Low Velocity Impact Testing. C scan measurements, figure 4, indicate a slight increase in damage for the base materials under a tensile preload and a large increase in damages for carbon composite under a compressive preload. . The further development of impact performance models will enable automotive engineers to design and test composite .
low velocity impact testing
low speed impact testing
mmd4e moisture meter
Impact of Thermoplastic Composites: Testing and Modeling Presented at the 38th Annual Technical Conference of the American Society for Composites, . Ruggeri, Duane Revilock, Richard Martin and Wade Jackson for impact testing and post-test NDE support. 15 Acknowledgements. 16Tezara Cionita, in Natural Fibre Reinforced Vinyl Ester and Vinyl Polymer Composites, 2018. 9.4.3 Impact testing. The impact testing was performed by using ASTM D256. The specimen has a rectangular shape with dimension of 64×1.27×3 mm. The notch angle was prepared for 45 degrees with the notch depth of 2.54 mm. The impact test is designed to determine how a specimen of a known material such as polymers, ceramics, and composites will respond to a suddenly applied stress. The impact test is explicitly used for evaluating the toughness, brittleness, notch sensitivity, and impact strength of engineering materials to resist high-rate loading [8,9].
Various impact tests, including Charpy, Izod, and drop weight testing, assess the impact resistance of metals, plastics, and composites used in car bodies, bumpers, and interior components. For example, drop weight testing simulates real-world crash scenarios to evaluate automotive components' energy absorption and deformation during collisions. One of the problems with composites is their weak impact damage resistance and post-impact mechanical properties. Composites are prone to delamination damage when impacted by low-speed projectiles because of the weak through-thickness strength. To combat the problem of delamination damage, composite parts are often over-designed with extra .the performance of polymer, composite, and light alloy materials when subjected to an impact. Selecting the . An impact test determines a material’s resistance to an impact event. It measures the amount of energy the material absorbs when it is hit by a high-rate load. The most common impact test methods are Charpy
The ASTM D8388 sandwich FAI test was published as a standard practice rather than a standard test method, as it supplements the existing ASTM D7249 4 long beam flexure test method for use with impact-damaged .The Charpy impact test is a standardized mechanical test conducted at a high strain rate and aimed at measuring the amount of energy absorbed by a material during fracture. . Fibre-Reinforced Composites and Hybrid Composites, 2019. 1.2.3 Impact test. The impact test is designed to determine how a specimen of a known material such as polymers .
The effects of specimen inertia on the instrumented impact testing of cementitious composites are discussed and a method for reducing such effects is proposed. A two degree of freedom model capable of predicting the amplitude and period of inertial loading oscillations on the tup-load versus time-trace is presented. Results of tests conducted on asbestos cement and fiber .
Fig. 4 shows the test samples after the impact testing is done. Fig. 5 shows the variation of impact strength in KJ/m 2 with respect to the variation in the weight percentage of Nano clay and fiber orientation It was observed that for 3.5% clay loading the samples showed an increase of 24%. The improvement in the nanoclay based materials may be due to the . This highlights the golden rule of compression testing of composites: It is not what method you choose, so much as ensuring it is used correctly that leads to accurate and reliable test results. Figure 6 – Compressive strengths of various unidirection carbon/epoxy composites as a function of slenderness ratio using different test types [7] In a low velocity impact test, hybrid composites with Kevlar fibre comprising the outer layers have lower impact properties than those with kenaf fibre as outer layers [44]. It has also been determined that hybrid Kevlar-kenaf composites absorbed more penetration energy than the individual kenaf/epoxy composites and Kevlar/epoxy composites in .
A 91-cm (36 in.) diameter full-ring subcomponent was proposed for larger scale testing of these and other composite concepts. Explicit, transient, finite-element analyses indicated that a full-ring test is needed to simulate complete impact dynamics, but simpler tests using smaller ring sections are adequate when the evaluation of initial . The escalating use of fiber-reinforced composites (FRCs) in aerospace, defense, automotive, and renewable energy industries underscores the need for a comprehensive understanding of their impact resistance and damage tolerance. This review meticulously examines low-velocity impact (LVI) on FRCs, covering impact mechanics, velocity .The projectile shape and impact velocity are often selected based on blade speed and failure modes observed in a particular engine. However, detailed analysis of both the test method and the full engine case design is needed in order to properly evaluate the test data. The desired result from the impact test depends on the containment Background Ultra high molecular weight polyethylene composites are fiber based composites used in armor applications. While some characterization has been conducted experimentally, this study varies multiple parameters simultaneously to investigate material response under a wide range of conditions. Objective This work focuses on characterizing the .
cimen. Very recently, however, another tensile impact test using the SHPB technique has been successfully developed at Oxford. Specimen design closely follows the pro posals of Ewins (12), which have gained widespread acceptance for the quasi-static tension testing of carbon/epoxy composites (1^). The testing technique is similar to
Boeing and Airbus developed a special testing procedure to investigate the compressive response of laminates that have been impacted (following standards ASTM D 7137 and DIN 65561). This study focuses on both experimental and numerical analysis of Kevlar plates subjected to compression after impact. To ensure high quality and appropriate mechanical .
moisture meter air
impact testing process
Resultado da 23 de jun. de 2022 · Versão desenho animado da Batalha de Youtubers Jooj Natu Vs. Mussoumano.• baixe grátis o Mussoumano Game: .
impact testing composites|impact testing examples